When you choose an automatic packaging machine, whether it is liquid, solid, or granular, you usually face two choices, Premade Pouch Packing Machine and Form Fill Seal Machine. Below we will compare the advantages and disadvantages of the two for your judgment suitable packaging machine.
Speed
In terms of speed, both Premade Pouch Packing Machine and Form Fill Seal Machine have good performance. After all, they have evolved over decades. The current high-speed Premade Pouch Packing Machine and Form Fill Seal Machine can reach the highest Faster packaging speed of 60-100.
The packaging speed has a lot to do with your materials because usually the final packaging speed is determined by the weighing and filling equipment. If the feeding speed cannot keep up with the fast sealing speed, it will not help. Another important factor is the style of the packaging bag. Complex packaging bags will slow down the packaging speed because there are more steps than simple packaging bags. There are many products on the market that are optimized for speed, but usually, the price will be much higher, and the accuracy of packaging will decrease. So please remember that fast is not necessarily good. It is the most important thing to be able to meet the unique packaging needs of your products because you can increase the speed by buying multiple machines and configuring multiple product lines. Of course, this also needs to be based on your plant space to decide.
All in all, the Form Fill Seal Machine has the upper hand in speed, but there are many ways to make up for this, speed is not the most important.
Exterior
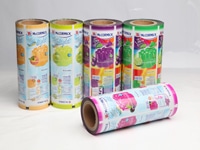
In terms of appearance, Premade Pouch Packing Machine undoubtedly beats Form Fill Seal Machine. Using Premade Pouch Packing Machine allows you to stand out in appearance and user ease of use, such as spout pouch, zipper pouch, stand up pouch, and so on. If you want to get this advantage, you must choose Premade Pouch Packing Machine. In addition, even for the pillow bag that Form Fill Seal Machine is good at, using Premade Pouch Packing Machine packaging will still be more beautiful than Form Fill Seal Machine, because Premade Pouch Packing Machine uses Premade Pouch, which makes the edge of the bag more neat and beautiful. The Form Fill Seal Machine will use a large roll of Rollstock to seal the edges while feeding, so the edges are not neatly sealed.
All in all, Premade Pouch Packing Machine can pack many bags that Form Fill Seal Machine cannot pack. Even if Form Fill Seal Machine can pack, Premade Pouch Packing Machine far exceeds Form Fill Seal Machine in appearance.
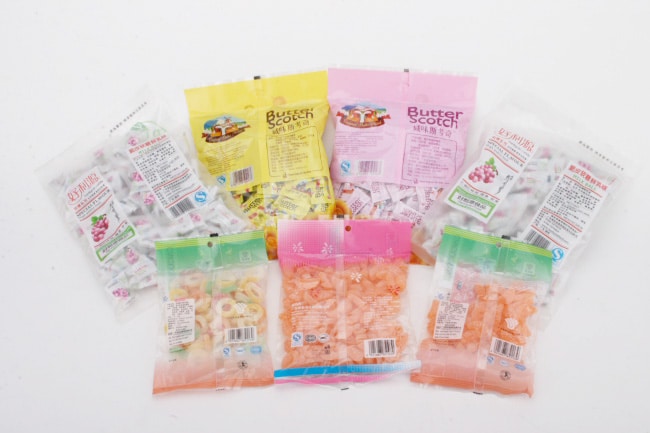
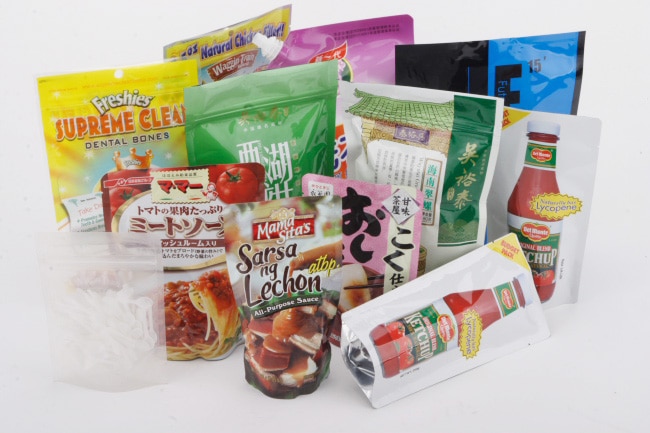
Cost
No matter when the price is a very important factor. Although the cost involved in the entire packaging process is very difficult to calculate, in general, the price of Premade Pouch Packing Machine will be higher than that of Form Fill Seal Machine. We will calculate the packaging below. Cost in each process:
Machine
The first is the cost of the machine. There is no doubt that the price of Premade Pouch Packing Machine is higher than that of Form Fill Seal Machine because it is more complicated.
Packaging Materials
The second is the cost of packaging materials. We learned from the packaging material manufacturers we cooperated with that the price of Premade Pouch for each packaging bag is higher than Rollstock. This is easy to understand. After all, Premade Pouch will have more processes, but in the long run, You will also bear some additional costs on Rollstock, such as higher labor costs and the disposal of Rollstock waste. However, there are some advantages of using Rollstock, such as being more flexible. When changing the packaging, the same Rollstock can be packed in many different sizes, and the Premade Pouch Packing Machine may leave you with a large amount of inventory, which you may not be able to use. The Premade Pouch of the previous product caused waste. In addition, some premade pouch packaging machines (including ours) have safety systems: no bag open, no filling, and sealing, wrong bag open, will not enter the next process, increase the bag using rate. Vertical packing machine will cause waste.
All in all, the price of Premade Pouch Packing Machine will be higher than that of Form Fill Seal Machine, whether it is the cost of the machine or the cost of packaging materials.
Operability
In terms of operability, I think you don’t have to worry about it. After years of development, most of the machines are already very easy to operate. Our machines are equipped with detailed instructions. At the same time, we can also guide the operators on-site, although the Premade Pouch Packing Machine There are indeed many differences in the operation of the Form Fill Seal Machine, you should not decide your choice because of this.
Other
Although there are still many places that can be compared, such as accuracy, stability, power consumption, volume, etc., they are all related to the different solutions of different machinery companies. Most of them cannot be compared objectively. However, for Echo Machinery, our Premade Pouch Packing Machine will have more advantages.
TL;DR
If you have enough budget, or you are a relatively high-end product in the industry, you should choose Premade Pouch Packing Machine, otherwise, you should choose Form Fill Seal Machine. If you have any questions about this, please consult our customer service staff. We tailor the corresponding production line for you according to your industry.